Our Tube Manipulation Capabilities
- 4 mm (1/8″) to 76 mm (3″) diameter CNC tube and bar bending
- Up to 50 mm by 50 mm rectangular tube
- Extensive range of draw bend radius tooling
- CNC multi-stack for multiple radii
- CNC push bending for larger radii
- Combined CNC draw and push bender for complex solutions
- NC, manual machines and hand bending for small diameter tube and complex solutions
- Mild steel, aluminium, copper, stainless steel and cupro-nickel (kunifer)
Benefits of tube manipulation
Rigid tube offers a more robust, longer life, often lower total cost solution compared to flexible hose and is visually more appealing. Complex bend paths or hose/tube combinations can eliminate multiple components and leak paths. Of course, via our other divisions, we can also offer you the full range of flexible hose for when that is most suitable, so the choice is yours!
Design for Manufacture
Design for manufacture
We have a very extensive range of tooling and can therefore often avoid charging tooling costs. However, if you have the opportunity to speak to us before the design is finalised, we can work with you to find the most effective solution.
Standard tooling and guidelines are:
- Bend radius is 2 x tube diameter
- Keep all bends to the same radii, or ideally a maximum of two radii
- For large arcs, to be formed using push bending, radius should be more than 7 x diameter
For more detailed tube manipulation design guidelines click the button below.
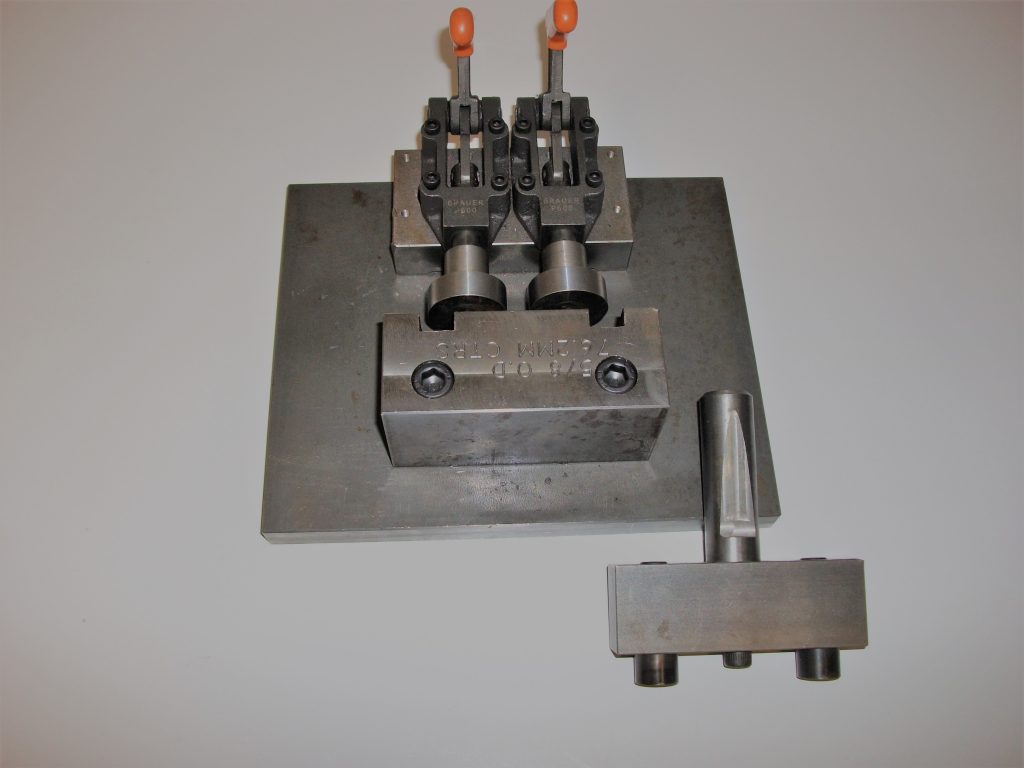
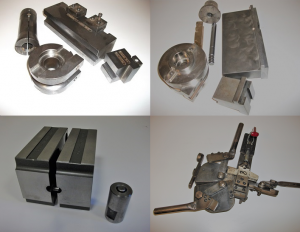
Mandrel Bending
We provide mandrel bending to overcome material wrinkling or collapse during forming which can occur with some tubing of thin wall relative to its diameter or based on material specification.
Using our draw bending process it is possible to support the tube at the point where the bending is taking place by inserting a mandrel down the centre of the tube. With our extensive range and access to mandrel bending tooling we are able to handle any such bending task.
Normally the mandrel is a straight rod with a hemispherical end. In the more demanding applications a flexible mandrel is used which can flex in all planes reducing wrinkling, stress and breaking during the bending process and allow for bends of multiple different directions and angles.
Those bends below two times the diameter of the tube usually require mandrel bending. Using the correct mandrel we can achieve bend radii as tight as the tube diameter with close to zero deformations depending on wall thickness, material specification and tooling availability.
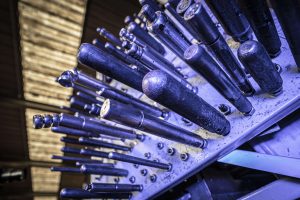
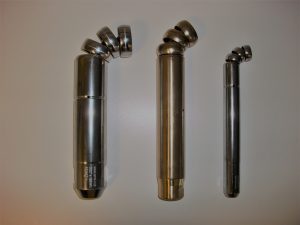
Advantages of Mandrel Bending:
The advantages mandrel bending offers are:-
- no reduction in flow volume caused by wrinkles in air and gas flow tube applications
- tubes are bent blemish free in their original, pristine shape
- additional stresses leading to tube fracture are avoided
Exhaust systems, piping systems, roll cage (ROPS & FOPS) and certain aircraft applications are often suited to using mandrel bending to achieve the integrity required although any applications with tight bend radii, thin-wall tube and exotic hard to bend materials are candidates. Based on our production knowledge and experience we will ensure mandrel bending is selected for such applications to ensure your products fully meet specification.
Roll bending
In addition to draw bending, with or without a mandrel, we also offer roll bending, sometimes called push bending. This is particularly relevant when you need large sweeping curves.
Draw bending pulls or “draws” the tube around a former. Once the required radius of the bend becomes large, say 7 times the diameter of the tube, the size of the draw bending former (not to mention the cost) becomes excessive.
In contrast, with roll bending the tube is passed through the gap between two rollers on one side and one on the other. As the tube is moved, either by being pushed from the end, or by one of the rollers driving it, and pressure is applied between the roller set, the tube is forced into a curved shape. The more the pressure the tighter the curve, and the smaller the bend radius. This means that one set of tools can produce many different bend radii. Typically, suitable for bend radii from 7 times tube diameter, this forming method suits applications such as handrails, guards, support tracks, architectural installations, and the production of large tube circles.
We have two types of roll bending machine, to suit different requirements. The standalone roll bender can produce simple arcs, in a single plane, in sizes up to 75mm. This meets most needs and tooling costs are relatively low.
However, we also have the capability to produce roll bent sweeping arcs on a CNC bending machine that can also perform draw bending. This allows for both small and large radii bends within the same component. It is also possible to have roll bends in different planes, and most interestingly, to produce a helix. Helices, of course, are relevant to many industries, but in particular where heat exchangers are required.
In terms of design considerations, because the roll bending rollers and the draw bending formers both have to occupy space on the tool stack you should ensure that if there are multiple draw bendings required that you maintain the same radii throughout your component (which anyway is always good tube design practice). In addition, you should always allow sufficient straight clamp space between bends, whether roll or draw. For further information please download our design guides or contact us directly.